Four Ways To Maximise Commercial Loading Dock Door Efficiency
The loading dock is where most warehouse operations begin and end. It is where goods are prepared for shipping or received. The loading dock gets a fair share of personnel, product, equipment and vehicle traffic on a daily basis. This is the reason loading docks must be designed with productivity and efficiency in mind.
Businesses will gain a lot from a loading dock that is designed for the optimal flow of operations. It reduces total turnaround time, staff effort and operational costs.
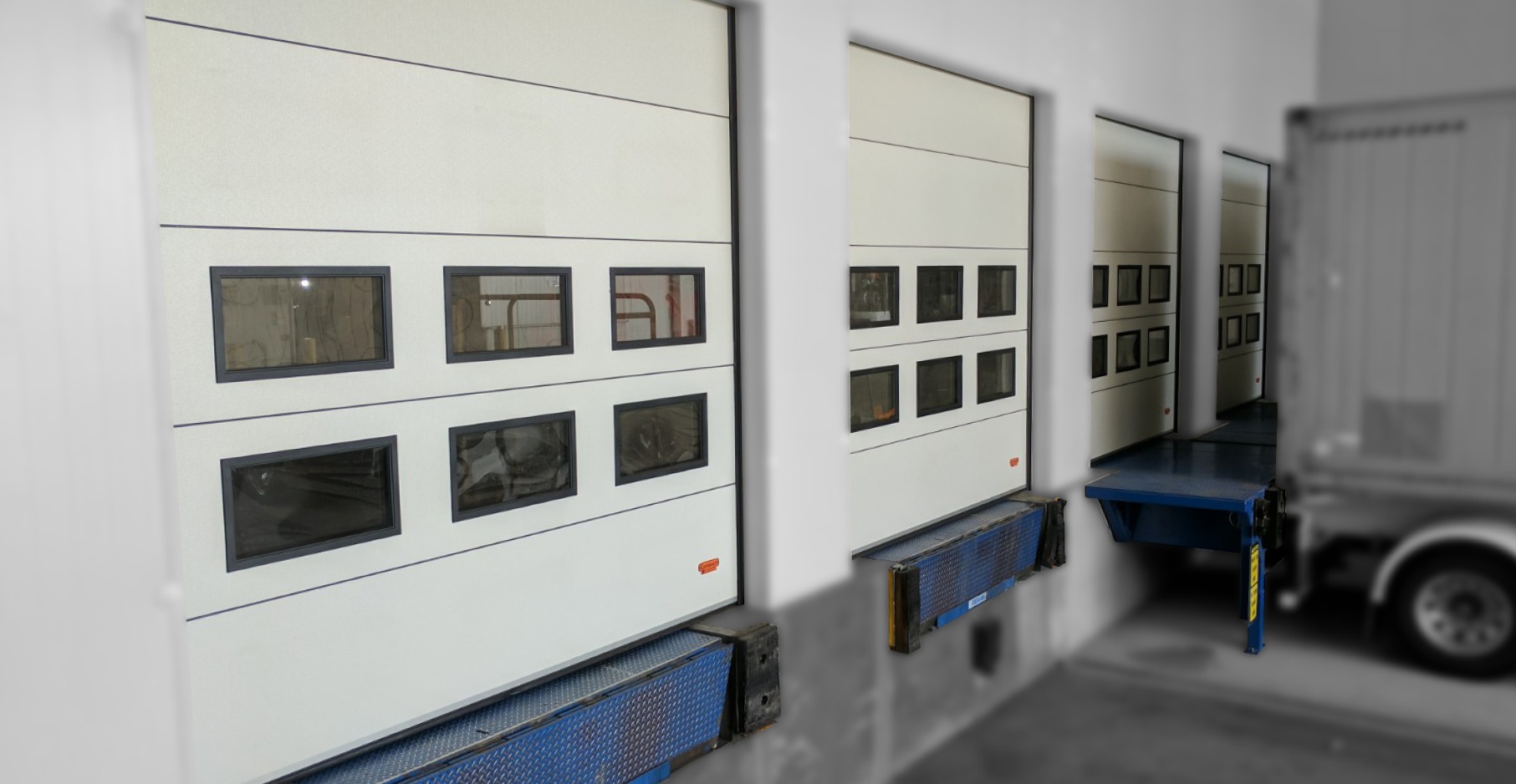
1. TRAFFIC-BASED LOADING DOCK LAYOUT
On top of complying with Traffic Engineering design standards and local council codes, the layout of the loading dock should focus on creating strategic space and pathways through which personnel, products, equipment and vehicles can move easily.
Decide whether the roadway approach or the yard approach is most suitable for the warehouse location as this is the first step in creating the pathways at the loading dock. Property gates should measure 4.8 to 6 metres (16 to 20 feet) for one-way traffic roadways and 9 to 9.7 metres (30 to 32 feet) for two-way traffic roadways. An additional 1.2 metre (4 feet) should be included if operations require walkways for pedestrians with equipment.
2. APRON SPACE
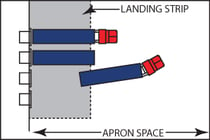
The apron space must take into account the movement of the trucks and trailers, as well as the space required to achieve the movement.
Make sure that the apron space is surfaced with asphalt or concrete rather than gravel to create an even, concrete landing strip.
3. LOADING DOCK DOOR SYSTEMS
The door systems of loading docks should be able to handle heavy-duty traffic and should be low maintenance to maximise its worth. Whether you have a flush loading dock, enclosed loading dock, open loading dock or sawtooth loading dock, consider the height and width of the door and the incline of the platform to match the truck and trailers.
When it comes to door systems, consider choosing between a manual and a powered door. Whilst a powered door consumes more energy, it essentially reduces the time and effort of the staff to open and close doors. Saving time that delivery drivers are waiting at dock doors, allowing for a quick turnaround as well as ensuring that doors are indeed closed once a delivery has been made. In contrast to automated doors, human error could mean that doors are left open longer than they need to be, losing temperature controlled energy from within the site.
Warehouse door systems should be closed when not in use to ensure regulated temperature, a controlled environment and minimal airborne contaminants. Consider automation of the closing sequence through integration with loading dock equipment, or just the integral timers in the door control system. The Compact Sectional Door is one such insulated dock door system that allows for automation.
The sectional insulated door are all-purpose and durable door systems suitable for any building. They are typically floor-to-ceiling, allowing trucks and trailers full access to the building, and personnel to the trucks and trailers. This will essentially ease the task of loading and unloading goods. Roller shutters come in various slat types, such as standard, perforated or slotted, to suit the building's ventilation requirements.
Sectional insulated doors are used more commonly than roller shutters for docks with insulation or controlled temperature considerations. With varying panel thickness to cater for a wide range of temperature requirements, a sectional insulated door provides a very effective thermal barrier when closed, to maintain your dock at optimum operating temperature. Consider temperature control with frequent door open as well as insulated rapid roller door.
View the full Movidor rapid roller door warehouse range here: Movidor Rapid Roller Door Range.
4. LOADING DOCK BUMPERS
Dock bumpers are crucial safety measurements for loading docks. The size and position of the bumpers are the keys to preventing damage to the building and the vehicles. Dock bumpers measuring 25.4 centimeters (10 inches) are the most commonly used for loading docks that are approximately equal to the height and width of the trucks and trailers.
When designing the loading dock for efficiency, focus on ease of access and safety. The personnel must be able to transfer and store products through a clear pathway. The vehicle drivers should be able to come in and out of the loading dock in an organised fashion to reduce time and risks.
Remax Doors offers durable and reliable doorway systems for all commercial and industrial buildings. We design and build a customised system to suit the needs of your facility. We help ensure the safety and efficiency of workplace operations.
Remax Doors offers a complete project management service and can oversee the removal of old, redundant door systems, including the electrical disconnection and making good of damaged doorways. That way, installation of new dock doors or barriers can proceed smoothly, right through to integration with dock levellers and inflatable dock seals.
Get in touch with us today to discuss your dock door requirements; alternatively organize a Site Assessment where our team will attend site to consider what will be the best solution for your site. Call 1800 010 221 or email: info@remaxdoors.com