How to reduce the heat in your warehouse during summer
Tips to help you save money and increase efficiency in your warehouse
It can prove daunting to decipher exactly where to find savings on heating or cooling your warehouse. So what is the best solution for your particular site?
The two biggest energy consumers in a warehouse are lighting and temperature control (in the form of heating, cooling or refrigeration). In fact, they account for approximately 76 percent of total energy use, which makes these systems the best targets for energy savings.
With some simple steps, you can not only save yourself money, but also increase the efficiency of your warehouse.
1) Install doors with good insulation
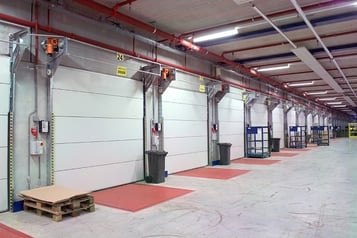
This may sound obvious, but for many warehouses, insulated doors are not a priority. That's even though the energy loss through them could be significant when you consider the amount of wall space which they could consume.
Consider all your options and the insulation values of warehouse doors on offer before you make a final decision - the cost savings may be significant.
Notice in the picture above that the door panels fold up into small, compact units above the doorway, which allows lighting to be installed directly above them.
Standard overhead doors often require hefty overhead beams for the door to roll up and over, which eliminates any chance of having overhead lighting or ducting right above the doorway.
2. Close the door!
One of the biggest loads on an air conditioning is infiltration, defined as the leakage of outdoor air into a conditioned space. Infiltration is even more costly for cold-storage warehouses, walk-in coolers and blast freezers. It can also create an uncomfortable workplace for your employees in the depths of summer and/or winter.
All of this is why insulated doors are necessary for any warehouse trying to maintain a strict interior temperature and lower their energy costs. An open door provides the largest portal for energy loss in any warehouse. To counteract this (since your employees will need to come and go throughout the day), consider opting for doors that are automated, high-speed and easily repaired.
Having doors which are operated by sensors, and which will open and close straight away after personnel have moved through, will cut down significantly on the energy lost when doors are left open for longer than required.
3) Upgrade your warehouse lighting
With lighting, the experts suggest starting with two questions:
1) How much light is necessary in the warehouse?
2) Where is it needed most?
Clearly, automated warehouses (where there is little human activity) require much less lighting than a fully staffed facility. Also, a clerk’s station requires a different kind of lighting than a warehouse floor.
“Think about how warehouses work. Many don’t have people in them,” says Lindsay Audin, president of energy consulting firm Energywiz Inc. “There are robotic warehouses with automated trolleys and robotic forklifts that can operate in the dark.”
By adopting more efficient lighting systems, your warehouse can save as much as 50% on your energy bill.
Fluorescent fixtures turn on immediately, eliminating the long warm-up cycle of HID lighting (which is often the reason for leaving HID lamps on even when the light isn’t needed). The downside to fluorescent lamps is that light output might be less than some HID systems, such as metal halide. Historically, fluorescent products have also had a shorter life than HID lamps. With recent advances in fluorescent technology, however, the gap is closing.
Motion sensors can also extend lamp life. One way to improve light levels while reducing energy expenses is simply by keeping the fixtures clean. Painting warehouse walls white and installing windows and skylights to introduce natural light help too.
And speaking of natural light in warehouses: while skylights are becoming commonplace because of exhaust requirements, the daylight they bring in is an extra benefit. Thermal glass in the skylights can help maintain climate control too. Glazed skylights on north and south facing walls can help provide the optimal diffused daylight needed for a well illuminated warehouse. Diffused daylight is a better light source than lighting as it doesn’t cast the same shadows that overhead lights do and it reaches more of the warehouse.
The benefits don't stop there: daylight in the workplace is also associated with higher worker production and morale. By matching a photo-control system to well-designed skylights you can have auto adjusting lights to keep your warehouse illuminated as the daylight fades while saving money during the day.
Check out and download our eBook on 20 Common Problems Found During Energy Audits.
4) Consider cool roof technology for your warehouse
Next to lighting, experts say a warehouse roof can be one of the biggest sources of energy inefficiency. Warehouse roofs are notorious for soaking up solar heat. While a facility’s ability to absorb heat might be advantageous for some facilities in the winter, it often means wasted money overall.
Depending on your warehouse’s purpose, cool roof technologies could cut down on energy costs. Cool roof systems have two critical properties:
1) A high solar reflectance, which means they absorb less energy from the sun, and
2) A high thermal emittance, which means they radiate a large percentage of the energy they do absorb back to the sky.
Regardless of climate, cool roof technologies are highly beneficial for warehouses with refrigeration storage, which demand consistent year-round cooling regardless of their location. Cool roofing technologies can improve energy efficiency in these facilities by 5 to 10 percent.
Dry storage warehouses typically don’t have refrigeration year round, yet they still require a consistent temperature. In these settings, cool roofing systems can contribute an even higher percentage of cost savings.
In buildings with no air conditioning, cool roof systems make the building more comfortable for your workers. Since refrigeration and air conditioning are heavy strains on the power grid, cool roofing technologies can reduce peak demands and improve the load on the utility grid.
Note that while cool roof technology can reduce your energy consumption in the summer, it also can increase energy consumption in the winter. In the winter there is value in heat gathering - you need to model the behavior of the building in all climates.
When considering a roof change, you need to look at the overall impact. Depending on where you are, you might lose energy more by getting rid of heat. In calculating the energy savings from reduced cooling load and the energy penalty from reduced winter heat gain, it’s important to take into account rising costs of both heating fuel and electricity.
While cool roofing technologies can reduce cooling costs, not all products are created equal. Energy Star roofing and coating products are good reflectors of solar heat, but not all coatings are compatible with all existing roof types. When selecting a cool roof, make sure the installer is experienced with the product selected.
Get more tips on reducing the heat in your warehouse
These quick tips aim to highlight some areas to consider changing in your warehouse and storage facilities. If you are interested in your cold storage options, contact Remax Doors online or call us on 1800 010 221.