Rapid Roller Door Service Cost: Repair and Maintenance
What Does Roller Door Repair and Maintenance Cost?
Rapid Roller Door service cost can vary significantly depending on several factors, for example, is it a routine roller door maintenance or roller door repair; the extent of the damage; the type of the roller door (is it a commercial garage door, commercial roller shutter, commercial roller door or high-speed warehouse roller door repairs), and the quality of the manufacture - think how often you need roller door repair or maintenance.
The location of the roller door service affects costs because labour rates vary by region. If the roller door service is urgent and requires a fast response, you might incur extra charges for the rapid roller door services. It's also important to consider if any parts need to be replaced during the service, as the quality and brand of those parts can further influence the price.
In this post, we look at some of the most common factors that affect the cost of commercial or industrial roller door repair.
To get the most accurate estimate tailored to your specific needs, it's advisable to consult with a qualified technician who specialises in Rapid Roller Doors Repairs and Maintenance.
Here are Five tips for understanding the cost of rapid door maintenance and repairs
Rapid doors often enable the critical pathways into your facility. That's why it's essential that you ensure they are:
- Appropriate for their intended use
- Secure, and
- In good working order.
If you are having problems with your current rapid doors, then you need to have a professional determine if it can be repaired or if it will need to be replaced.
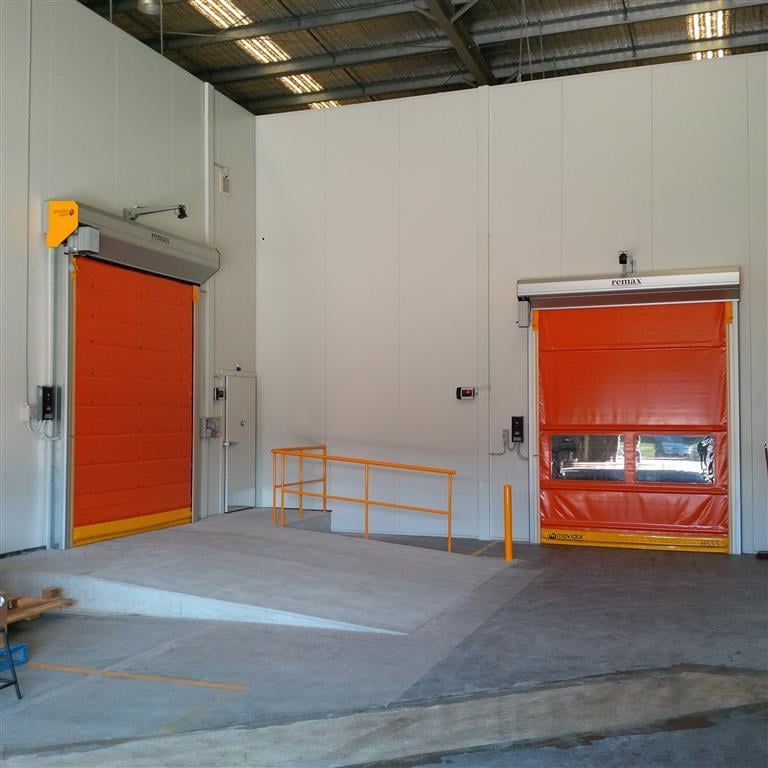
1) What Do Some Common Rapid Door Repairs Cost?
To be in a position to provide your facilities with onsite support and service to critical doorways, it's a good idea to conduct your own basic roller door servicing and inspections.
However, it's also good practice to schedule routine inspections with a professional, such as an industrial door supplier, since they will have good knowledge of the doors and any possible related issues, and will also carry a stock of spare parts. An industrial door supplier may also be able to upgrade your equipment if and when the doors require replacement.
A typical service call will include a manual inspection of the door and opener. Then adjustments can be made including limits and force adjustments and door and motor lubrication.
Fees for a rapid door service call could vary from $95+gst for an inspection, up to $300+gst for inspection and service. By comparison, a repair bill when something goes wrong with your door can run to anything from $1,500 up to $6,000, depending on the nature of the damage or failures.
Here are some common rapid door problems and the associated cost of repair:
a) The Rapid Roller Door Will Not Open or Close
There could be several reasons for your rapid door to stick in one position or another:
Photocell sensor obstruction – most automatic doors are equipped with photoelectric sensors at the base of the track to provide safety for pedestrians. Any obstruction could make your rapid door fail to operate correctly.
Check to be sure there is nothing in the path or across the face of the sensors. It's not uncommon for service technicians to be called to a malfunctioning door, only to remove a spiderweb or a jacket left by a visitor onsite covering the photoelectric sensors!
Remote control issues – If your door is connected to remote controls, it may be worth checking their battery and the frequency programming. If there is a small light on your remote, press the button and see if the light illuminates.
If it doesn't, you will likely need to replace the battery inside the opener, or re-program the remote to the receiver card. This is a very inexpensive repair, and may solve the problem without a service call.
Track obstruction – Sometimes accidental damage to the door guides can be enough to cause the door to jam or bind during operation. Examine the tracks for potential damage like dents and kinks; and look at your door curtain in the open position to see if it is hanging unevenly. If the track is damaged or the door is hanging unevenly, it may be time to call a professional for repairs.
Replacement guides can typically cost up to $470 per side, depending on the door type and size. Costs for correcting the uneven hanging of rapid doors themselves can vary greatly, and is likely to require removal and realignment of the door head unit.
b) The Movement of the Rapid Door is Uneven or Jerky
Spring issues - Unless it's because of an obstruction of some type, uneven movement of your door could potentially be caused by a problem with the spring mechanism.
Many conventional rapid doors have 2-4 extension springs, holding tension on the door curtain. These springs are under significant tension and are dangerous if handled by untrained mechanics. That's why it's necessary to call a professional for any repairs to this type of spring mechanism to avoid serious injury.
Replacement of an extension spring or cables in a garage door or rapid door can take at least two or three hours of labor, and may require hire of access equipment such as a scissor lift.
Track issues - If your rapid door tracks are bent or warped in any way, your door will move unevenly or even refuse to move at all. Depending on the degree of damage, your tracks will need to be repaired or replaced. Refer to the details above relating to track obstruction.
Brake issues – Many automatic doors are electromechanically braked. These components work continuously at high inductive voltage and wear out over time. As they wear, it is not uncommon for relays and brake rectifiers to become faulty causing the brake to engage intermittently, which will show up as jerky door operation.
If this occurs it is recommended a door technician carry out repairs, which could range from $210 for a minor relay replacement, or up to $600 plus access equipment if the mechanical brake requires replacement.
c) Your Rapid Roller Door Makes Loud Noises When Opening or Closing
Lubrication Issue - Squealing, screeching, or grinding noises from your door may be indicative of a lack of lubricant or an accumulation of dirt or debris in the tracks. When removing debris, do not use harsh chemicals to clean the tracks. Once the track is clean, check with your supplier whether you should coat it with lubricant designed especially for rapid doors, if possible. Never lubricate door components without the instruction of the door manufacturer. Application of poor or incorrect lubricant may lead to further damage.
Misalignment Issue –If the door has been impacted, or a roller is damaged or broken, the door may operate with excessive noise and vibration. In this instance, it is recommended that a qualified Technician inspect and repair the door.
d) Your Rapid Roller Door Does not Hold Open, and Slides Down to Closed
Many non-counterbalanced doors may show this malfunction as an indication of brake problems. Motor brakes are not always expensive to repair, but should always be carried out by a qualified technician.
2) Other Rapid Roller Door Issues
Here are a few other issues that may arise, depending on the type of rapid door you have:
Torn or Broken Rapid Door Curtain
The major cost of this repair is the labour it takes to replace or repair the curtain.
Depending on the curtain material, most damage to a rapid door curtain can be repaired. However, for best results the door curtain should be removed and repaired in the door manufacturer’s factory, using high frequency welding equipment.
Removal of your damaged curtain means the door needs to be out of service for 1-2 days, and costs could run to $1,000 plus access equipment. Sometimes it is worthwhile replacing the entire door curtain at slightly higher cost, to minimise operational downtime. The Remax range of Movidor High Speed Doors are equipped to self-repair on impact, meaning that the door can realign the curtain into the curtain guides if it is knocked out of the guides by a hasty forklift or delivery driver.
Impact Damage
Depending on where the dents are and how badly dented the door is; dents to the door frame or curtain edge can cause other, bigger, issues with the rolling mechanism of the door.
Ask your supplier to visit site and assess the damage on-site. They may suggest new door frames, or a simple repair but it is worth getting it looked at in case it is affecting another element in your door, which could result in an even costlier repair.
Damaged Rapid Door Curtain Bottom Edges
There are many rapid action doors on the market with a hard bottom edge, which can be dangerous as well as expensive.
After a few incidents due to the excessive speed of the curtain and the stiffness of the embedded sensor, the European Community has implemented new regulations (EN 13241-1). Among the various normative constraints, the requirement against mechanical crushing during closure makes necessary to prevent contact with the door being closed or, in case of contact, to limit the vertical dynamic load below a strict curve. If the high-speed door does not meet one or more of these constraints, the closing speed will be limited to 0.5 m/s (1.64 ft/s).
Rapid Door Bottom Edge Replacement Cost
Repair costs to replace an impacted bottom edge can run to $2,000. Yet only a few manufacturers offering a fully flexible and harmless sealing edge kept possibility of closing at a higher speed. Movidor high speed doors have been engineered with a yellow soft edge which reduces the repair costs from vehicles and forklifts bumping into the door.
3) Total Cost of Ownership considerations (TCO), by door type
The goal in choosing a rapid door is to match the functionality required; and on a aesthetic level, to match the style of your facility.
There are several styles of rapid door to choose from. Here is a brief overview of a few popular rapid door styles and their advantages and disadvantages:
Rapid roller doors: High speed doors that are fast, robust and tough enough to handle a range of traffic, irrespective of the environment.
They cater for extra large openings, providing speedy access solutions even in wet environments as well as coolrooms.
Their short opening and closing times reduce cooling loss, avoid airflow and enable a smooth operating procedure. They can also be designed in larger dimensions for the mining and aircraft industries.
Movidor high speed roller doors are faster, safer and smarter, and designed to operate continuously in warehouses, distribution facilities, coolrooms, manufacturing facilities, car wash facilities and more.
The operate with minimal maintenance thanks to their self-repair feature which reacts to impact and relocates the curtain back into the guides.
Rapid doors are generally made-to-order for exact size and custom features, designed to be able to withstand equipment impact (break-away if accidentally hit by vehicle) and designed to sustain heavy usage with minimal maintenance.
Sectional doors (also known as a raised panel doors) are the most common doors in facilities such as loading docks, car showrooms automobile factories, car parking areas such as underground apartments, and residential garages. Sectional doors are made of several horizontal panels hinged together, fitted with wheels and mounted within a track.
The biggest advantage of this door is it takes up relatively little space, as you can see in this video on compact sectional doors. They are easily controlled with a standard remote garage door opener for a nominal cost. Their moving parts are readily accessible which can keep repair costs low.
The experience of many warehouse and distribution companies has proven that the Total Cost of Ownership (TCO) for operating and maintaining a high traffic-use door for its workable life is significantly higher than the purchase cost.
Damage from forklifts and other vehicles dramatically increases the TCO of the door. Where a steel roller shutter may cost $4,000-$5,000** to have installed, the cost to repair or replace bent metal slats, wind-locks etc, can amount to $500-1,000 per instance, not including downtime or production loss while the door is inoperable.
With some high speed doors, the costs can be significantly higher. Where a conventional high speed door may cost $12,000-$14,000 to install, costs to repair bent bottom bars, replace cables, springs or sensors, can easily amount to $2,000-$2,500 per visit. In some situations, it is not uncommon for companies to spend $5,000-$8,000 per annum for maintenance and repair costs for one door alone.
This need not be the case with proper evaluation of door design and activation options. Some high speed door equipment such as the Movidor range by Remax, while costing 10-15% more to install initially, have been designed to accommodate the accidental impact from forklifts, and will operate for millions of cycles, with minimal maintenance required. The Total Cost of Ownership of these doors is significantly lower, which quickly outweighs initial cost considerations.
Consider Rapid Door Finishes and Accessories
Before choosing a rapid door for your facility, think about the day to day activities that happen in your facility, such as:
- Do you need to regularly wash-down the area?
- Will your rapid door cope with being cleaned by pressure washers and harsh chemicals?
- Think about outside conditions and weather proofing against strong winds or drafts. Do you need to include ventilation panels in your door?
- Will you benefit from a including wicket door within your sectional door so that pedestrians can come and go without opening up the entire door?
- Do you need natural light in your facility even with the doors closed?
The Bottom Line on High Speed Rapid Roller Doors Repairs and Maintenance
Do you have ongoing concerns with the service / breakdown costs of your existing rapid Roller doors or fast action doors? The self-repair feature on all Movidor rapid doors can significantly reduce repair costs and downtime often associated with conventional hard-edge high speed doors.
In some cases, the annual spend on repairs and maintenance of problematic conventional high speed doors can be reassigned to new self-repairing flexible high speed doors, with a quick payback period.
Your rapid door is a major investment and entryway to your facility, which is why it's so important to keep them in good working order for your own safety, security, and convenience.
Choosing the right style and appropriate materials will reduce the amount of repairs that may arise, and thinking about the location and services offered by your supplier for quick call-outs, knowledge of the product, spare parts and future upgrades or assessments to improve the efficiency.
What's more, investing in regular maintenance can be cost-effective in the long run. If your rapid door is in need of major repair, it is best to call a professional door repair company for assistance. Typically, the company will charge for at least one hour for making a service call; however, the benefits of a professional repair job can well outweigh any costs, as a professional approach can ensure the safety, security, and proper operation of your rapid door.
Talk to us about high speed rapid doors for your facility
To find out more about rapid doors or any other Remax products please click here or call us on 1800 010 221.